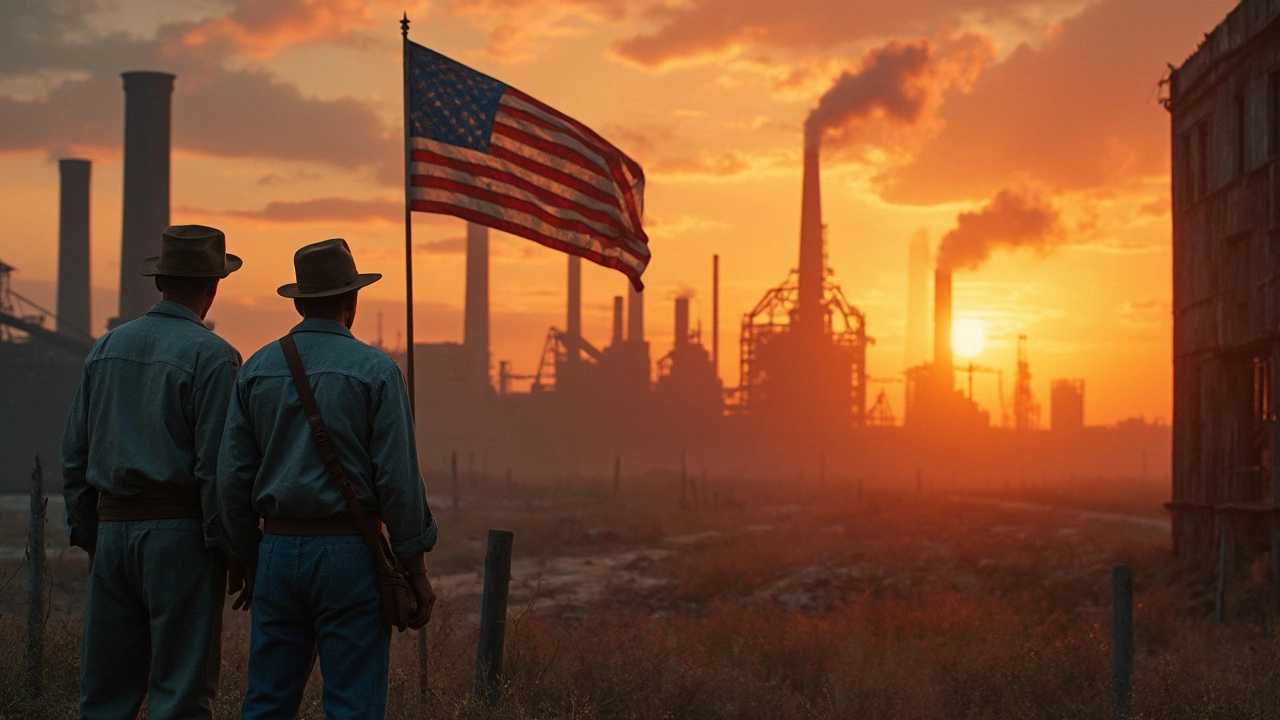
Not long ago, American steel was everywhere — the backbone of bridges, cars, and skyscrapers. But these days, old steel factories are quiet, and you’re way more likely to see steel stamped “Made in China” or “South Korea.” Ever wondered why?
The US didn’t just wake up one morning and decide to stop making steel. Over the last few decades, loads of things piled up. Costs went crazy. Other countries churned out steel for way less. And a lot of American plants clung to old methods while rivals got smarter and faster with new tech. That mix wrecked the business for many American mills.
If you’re eyeing a job in manufacturing or curious why steel towns aren’t bustling anymore, this history isn’t just trivia. It’s why some towns got left behind, and why buying American steel feels almost old-fashioned now. You’ll find some answers in changing global markets, but also in mistakes made right at home. Stick around — there’s more to this than just cheap imports.
- America's Steel Boom: What Changed?
- Biggest Reasons Factories Closed
- How Foreign Steel Got Cheaper
- Modern Tech vs. Old-School Plants
- What This Means for US Jobs and Economy
America's Steel Boom: What Changed?
Back in the mid-1900s, the US was the top dog in steel. American steel factories turned out more steel than anyone, enough to build highways, tanks, and washing machines for millions. Steel towns like Pittsburgh were booming, and the paychecks were solid. But if you fast-forward to now, those glory days are a thing of the past.
So, what actually changed? After World War II, the world rebuilt, and other countries like Japan and Germany caught up with better, faster plants. By the 1970s, the US was getting out-produced, and it only got worse. American factories stuck with old equipment, while other countries invested in new tech that made steel quicker and cheaper. Unions bargained for better pay and benefits, which was great for workers but also drove up costs. By the 1980s, US steel just couldn’t compete on price or speed.
Year | US Steel Production (million tons) | World Steel Production (million tons) |
---|---|---|
1950 | 87 | 189 |
1970 | 120 | 595 |
2023 | 80 | 1,888 |
See those numbers? US steel output pretty much stalled, while world production went sky-high. Today, China alone makes over half the world’s steel each year. The US steel industry slipped because it didn’t move fast enough or cheap enough to keep up.
- Other countries built new, efficient mills right after WWII.
- US stuck with older, expensive-to-run plants.
- Labor costs shot up in American plants.
- Foreign steelmakers got government support; US companies got hit with imports.
The bottom line—steel didn't disappear from America overnight. Big shifts in technology, global economics, and even local politics pushed the glory days out and brought in tough competition from overseas. That's what changed for good.
Biggest Reasons Factories Closed
The downfall of the US steel industry isn’t just one story—it’s more like a pileup. Some of it was bad luck, and some of it came from moves that just didn’t pay off. Let’s break down why so many American steel plants shut their doors.
High Labor Costs: Back in the day, union wages at American mills were solid—folks could raise families on a steelworker’s paycheck. But those good wages made U.S. steel expensive compared to steel made in places like China, India, or Brazil, where labor costs were much lower. When every penny counts for big buyers (like car companies and builders), cost wins.
Rising Energy Bills: Steelmaking takes a ton of energy, especially using old blast furnaces that chew through power and resources. As natural gas and electricity bills soared in America, it put more pressure on already-struggling factories.
Foreign Competition: The world changed fast in the late 20th century. Overseas steel mills got help from their governments, churned out massive volumes, and sold it cheap—even below market cost. That "dumping" flooded American markets. In 2023, China alone produced over 1 billion tons of steel—more than half of the world’s total.
Outdated Equipment: A lot of U.S. factories stuck with machines from the 1960s and ‘70s. Upgrading would’ve cost millions, so companies made do. Meanwhile, new foreign mills built with cutting-edge tech could produce faster, cheaper, and with less waste.
Regulations and Red Tape: By the 1990s, American steel plants faced strict environmental rules. Cleaner air and water are a win, but the costs of meeting those rules stacked up. This made it even harder for old-school mills to turn a profit.
Year | US Steel Production (million tons) | China Steel Production (million tons) |
---|---|---|
1980 | 101.4 | 38.7 |
2000 | 101.8 | 128.5 |
2023 | 80.7 | 1,019.7 |
This data shows not just a slip, but a landslide. The U.S. stood still while China ramped up, pumping out steel for the world. For many aging American facilities, closing was just a matter of time.
- Steel output in the US fell by 20% between 2000 and 2023.
- In 1970, the US made about a quarter of the world's steel. By 2023, it was around 4%.
- Newer "mini-mills," which recycle scrap steel, helped a little by lowering costs, but not enough to bring back the old giants.
So if you drive past a rusting steel factory today, you’re not looking at random bad luck. It’s what happens when costs, global trade, and old technology all hit at once.
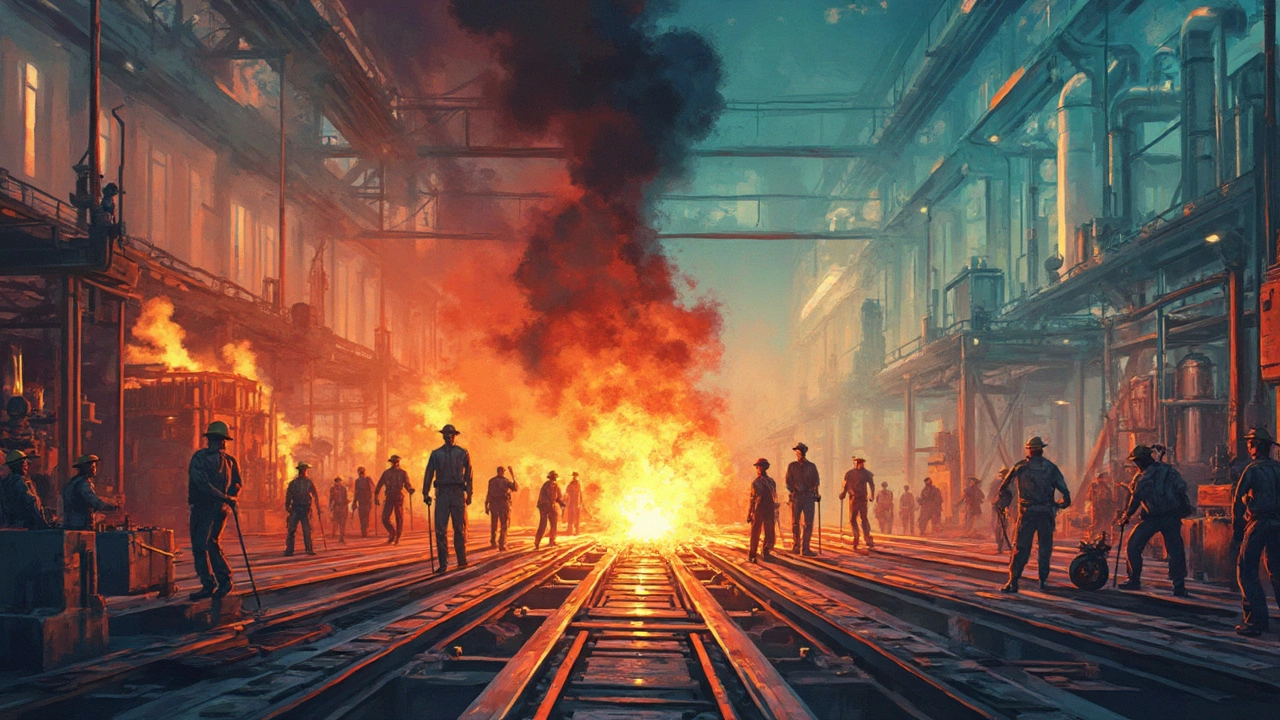
How Foreign Steel Got Cheaper
If you’re wondering why the US can’t compete in US steel anymore, the real shocker is how much cheaper other countries can make and sell it. One big reason? Government support. Countries like China and India have thrown mountains of cash at their steelmakers. They cut deals on electricity, land, and even loans. When you get your power almost for free and a loan with no strings attached, you can afford to crank out way more steel for a lower cost.
Another thing—labor costs kill American plants. Wages and benefits in the US are a lot higher than in places like Brazil, Vietnam, or Russia. So their steel comes off the line ready to sell at a price that most American companies just can’t match. Some countries also skip a few pricey rules about pollution or safety—stuff US mills have to cover with big budgets. That narrows the gap even more.
Trade policies play into this, too. Sometimes foreign governments dump steel—selling it abroad for less than it costs at home, just to grab a share of the market. The US government has tried tariffs to fight this, but those only go so far when the gap is huge to start with.
Country | Cost per Ton (USD) |
---|---|
United States | $650 |
China | $480 |
India | $510 |
Russia | $500 |
Brazil | $530 |
Check out that price difference. It’s no contest, especially if you’re a buyer who cares most about saving money. Some US companies still buy American-made steel for certain projects, but with those big numbers, most go looking elsewhere.
If you ever see a news headline about "cheap foreign steel flooding the market," this is the real breakdown. It’s not just about working harder or getting lucky—it’s about how the whole system is tilted, from government backing to costs that just don’t stack up.
Modern Tech vs. Old-School Plants
If you head inside what’s left of America’s old steel mills, you’ll spot giant machines that look like they’ve barely changed since the ‘70s. The problem? The world moved on, but the US steel industry didn't always keep up.
The big difference came with new technology—especially something called the “electric arc furnace,” or EAF. These furnaces are smaller, cheaper to run, and use scrap metal, which makes recycling way easier. Compare these to the old “blast furnaces” that gobbled up coal and iron ore, took up tons of space, and needed armies of workers just to keep running.
Check out how these two stack up:
Type | Fuel Source | Typical Workforce Size | Flexibility | Main Input |
---|---|---|---|---|
Blast Furnace | Coal & Iron Ore | Large | Low | Raw Ore |
Electric Arc Furnace (EAF) | Electricity | Small | High | Scrap Metal |
Here’s the thing: EAFs make up more than 70% of steel production in the US now, but for years, the industry was stuck with its old ways. That hesitation let other countries speed ahead. For example, China ramped up its EAF game and now owns more than half the world’s total steel output. It’s easier for these modern mills to crank out steel faster and cheaper with fewer workers. Some EAF plants run with just a couple hundred people, while old-school blast furnace setups can need over a thousand.
Old American mills also held onto union work rules and slow-to-upgrade equipment, which led to high costs compared to slick, automated factories overseas. That combination was brutal when global steel prices tanked. Suddenly, keeping these big old plants running no longer made sense, especially when new technology could do the job with less hassle and money.
If you’re thinking about the future, this shift also means fewer steel jobs now need college degrees and more tech skills. Want one tip? If you’re eyeing work in US steel, learning automation, robotics, or plant tech could make you way more hirable.
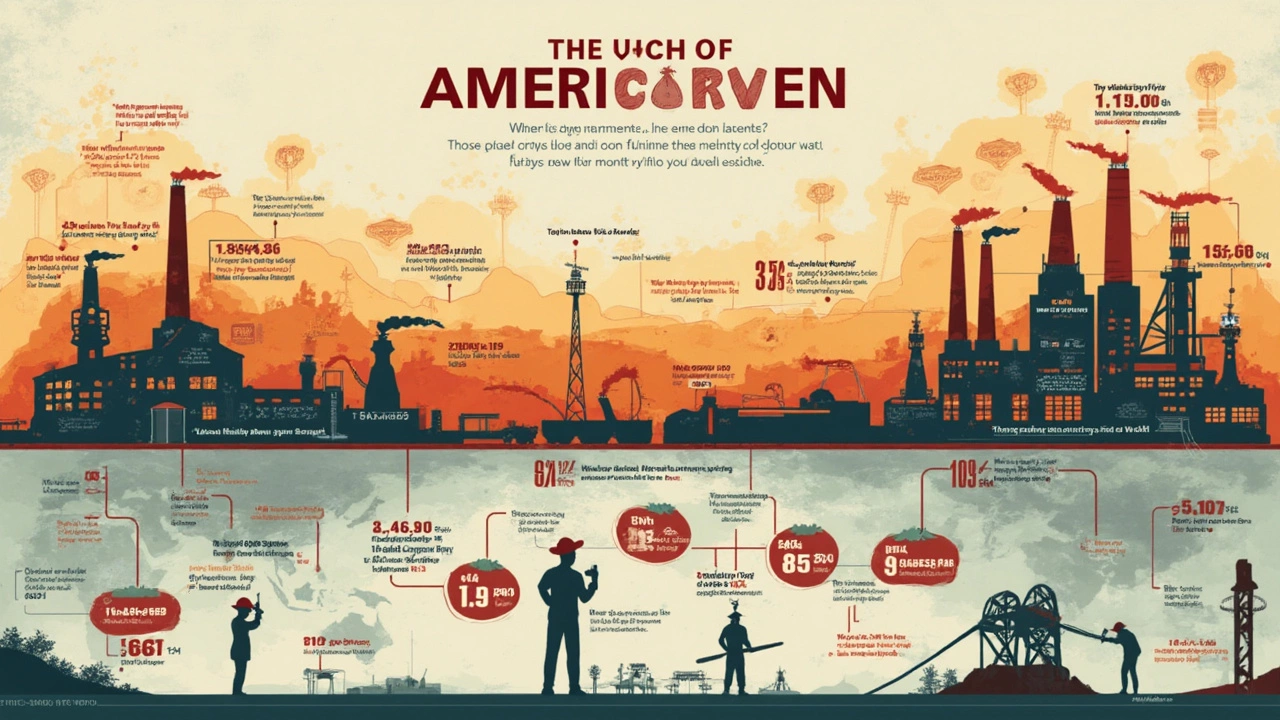
What This Means for US Jobs and Economy
The decline of US steel slams more than just the folks who used to pour molten metal on factory floors. We’re talking about thousands and thousands of workers in towns across the Midwest — places like Gary, Indiana; Youngstown, Ohio; and Pittsburgh, Pennsylvania. From the late 1970s to now, the number of jobs in steel dropped from nearly 400,000 to barely 90,000. When steel mills shut, local diners, repair shops, and suppliers got hit too. Those lost paychecks didn’t just disappear — they pulled down whole communities around them.
But there’s another side: steel is still used everywhere, from construction and shipping to making home appliances. With fewer big mills left, the US depends more on imported steel, which creates headaches for companies trying to plan and for folks worried about where things come from. Trade spats, like the tariffs put on imported steel in 2018, were meant to help US plants. Some mills did see a boost, but the bigger impact was higher prices for homegrown businesses that use steel — like car makers or appliance brands. Those costs often end up passed right along to the rest of us.
Towns that once thrived on steel have had to scramble. Some places brought in new tech jobs or green energy plants, but not everyone found an easy fix. Folks over 50 sometimes got stuck, since retraining for new work doesn’t happen overnight. Meanwhile, younger workers either moved or took lower-paying service jobs instead of good union factory gigs.
- Lower steel output means the US is more exposed if supply chains from overseas get disrupted.
- Communities hit by lost steel jobs usually take years — sometimes, generations — to recover, if they recover at all.
- Higher steel prices from tariffs can ripple through the whole economy, sometimes leading to layoffs in other industries.
So, the fall of steel jobs in the US isn’t just a business story. It’s something that shaped — and keeps shaping — the everyday lives of millions, changing what work looks like, and what security means for families linked to manufacturing.