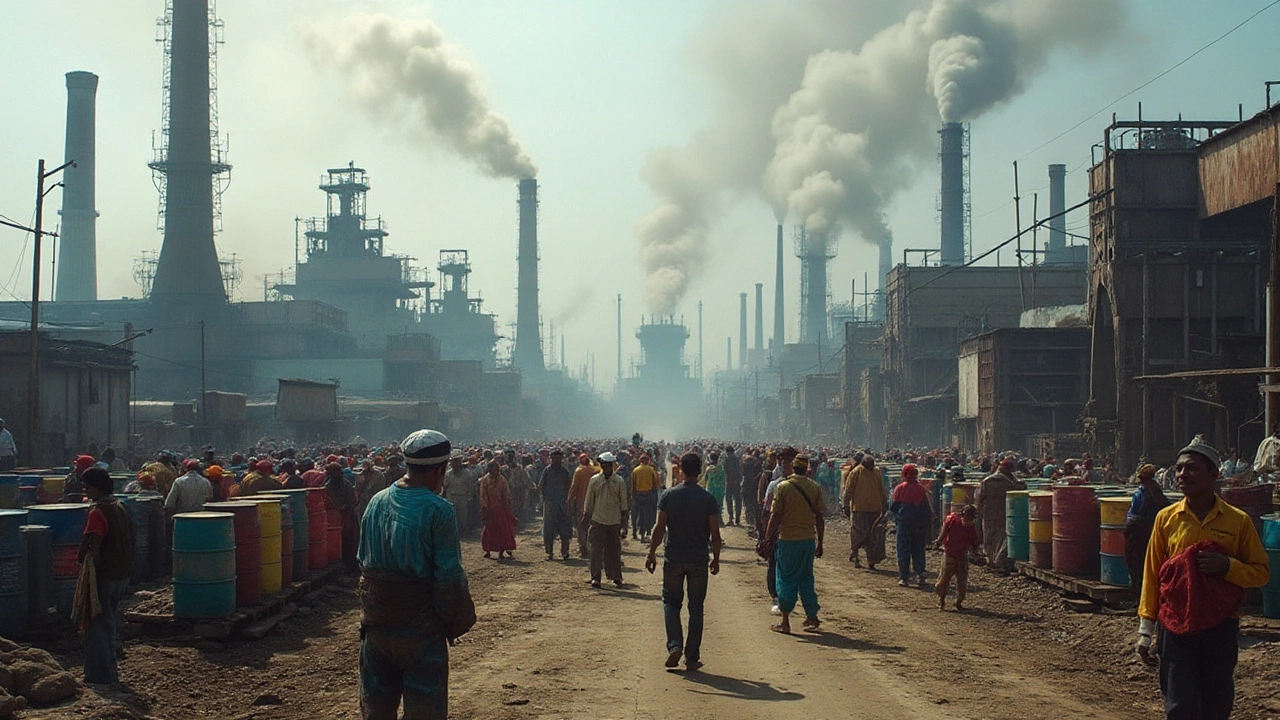
India, renowned for its bustling chemical manufacturing sector, finds itself in a tight spot as certain chemicals become increasingly scarce. This scarcity isn't just a minor hiccup; it's a significant strain on numerous industries that rely on a steady supply of these substances to keep their production lines humming.
The reasons for these shortages are multifaceted. Think of logistical snags, global demand shifts, and some geopolitical tensions thrown into the mix, creating a perfect storm that's hard to navigate. Businesses aren't just sitting ducks, though. They're actively seeking out innovative strategies to sidestep these hurdles, from diversifying suppliers to adopting cutting-edge technologies.
The stakes are high, as addressing these shortages isn't just about fixing the supply chain. It's about ensuring that India continues on its path of growth, contributing robustly to the global market. How this plays out could set benchmarks for how similar crises are handled worldwide, making it a narrative that commands attention from industry experts and policymakers alike.
- Current Chemical Shortages
- Impact on Industries
- Causes of the Shortages
- Strategies for Mitigation
- Future Outlook
Current Chemical Shortages
In recent months, the landscape of India's chemical industry has been dramatically reshaped by unforeseen shortages, causing ripples across various sectors. The bustling hub of chemical manufacturing is grappling with a scarcity of key components such as phosphoric acid, solvents like acetone, and essential industrial gases. These shortages are not merely numbers in a report; they represent real challenges for manufacturers who are struggling to maintain production schedules and meet market demands. For instance, the lack of phosphoric acid, crucial for India's vast fertilizer industry, has driven up costs and created anxiety among farmers who rely on timely and affordable supplies for their crops.
The burgeoning demand for these chemicals, both domestically and internationally, exacerbates the strain. As industries worldwide rev up production after the pandemic-induced slowdown, the global supply chain hasn't quite caught up, and Indian manufacturers are feeling the squeeze. The ripple effects are profound, impacting not just large-scale industrial operations but also small and medium enterprises that contribute significantly to the economy. "The shortage of key chemicals in India is akin to removing the foundation blocks of our industrial structure," mentions Dr. A. Kumar, a renowned expert in industrial supply chains. His words highlight the criticality of these materials to India's economic engine.
Industries such as pharmaceuticals, textiles, and electronics, which are major consumers of chemicals like acetone and other solvents, are particularly hard-hit. The electronics sector, reliant on solvents for manufacturing semiconductors, faces potential slowdowns just as demand for gadgets surges. In the textile industry, which often uses various chemical dyes and solvents, the shortage is causing delays in order fulfillment, thereby impacting international trade commitments. This shortage scenario is unlike any other, as it involves multiple interlinked factors—from logistical challenges at ports to limited availability of raw materials—and requires strategic thinking to navigate successfully.
Adding another layer of complexity, geopolitical tensions have disrupted traditional trade patterns, making it hard for Indian manufacturers to secure imports from neighboring countries that were once reliable partners. As countries adopt protectionist measures to safeguard their own industries, India must seek new avenues for sourcing these critical components. The dilemma puts the Indian government and industry players at a crossroads, requiring them to reevaluate and perhaps reinvent their sourcing strategies to safeguard industrial growth. This necessity has sparked widespread discussions on the potential of increased domestic production and innovation in chemical manufacturing.
The shortage of specific chemicals is not entirely unexpected, as similar scenarios have been observed historically; however, the scale and implications today are unprecedented. As industries brace for the worst, there is an urgent call for collaboration across sectors to develop resilient solutions that not only address the immediate issue but also strengthen the supply chain against future disruptions. This collaborative approach might include investing in research and development to find alternative chemicals or processes, thereby ensuring a sustainable future for India's chemical industry and securing its pivotal role in the global market.
Impact on Industries
The ongoing chemical shortage India faces is reshaping how various sectors operate, leading to significant disruptions. Industries across the spectrum are feeling the pinch, from pharmaceuticals, textiles, and agriculture, to more specialized fields like electronics and automotive manufacturing. These shortages trickle down through the supply chain, slowing production rates, escalating costs, and in some cases, leading to temporary plant shutdowns. The pharmaceutical industry, for instance, is grappling with a scarcity of essential raw materials crucial for drug manufacture. This not only hampers the ability to meet domestic demand but also affects India's role as a key exporter of generic medicines globally.
The agricultural sector is another critical area experiencing ripple effects due to shortages of fertilizers and pesticides, crucial chemicals that ensure crop health and yield. Farmers are left seeking alternative solutions, often at a greater cost, to maintain production levels. Similarly, the textile industry, a major contributor to India's GDP, is facing stiff challenges. Dye and textile chemical shortages are resulting in delays and increased production costs, pushing small to medium enterprises into a precarious position. Many businesses are forced to operate at reduced capacities, directly affecting profits and employment rates.
Automotive manufacturers aren't spared either. With shortages in specialty chemicals that are vital for manufacturing components, production lines are slowing, or worse, halting. This slowdown inevitably translates to longer delivery times and increased vehicle costs for consumers. A recent report by the Confederation of Indian Industry stated,
"The industrial landscape is rapidly evolving due to the persistent chemical shortages, an issue that requires immediate collaborative attention to protect India’s economic stability."This highlights a pressing need for industries to adapt swiftly, innovating to overcome these challenges and strategize effectively for the coming months.
Additionally, the electronics industry's growth is stunted because of the lack of certain chemicals used in circuit boards and chip manufacturing, leading to supply chain snarls in what was once a rapidly expanding sector. Faced with these circumstances, industries are exploring diverse strategies to mitigate impact. This includes engaging in long-term procurement contracts, developing synthetic alternatives, or investing in technology to optimize existing resources. Such steps are crucial in maintaining resilience amidst these turbulent times. The manner in which these issues are tackled today could very well define the trajectory of India manufacturers in the global market landscape.
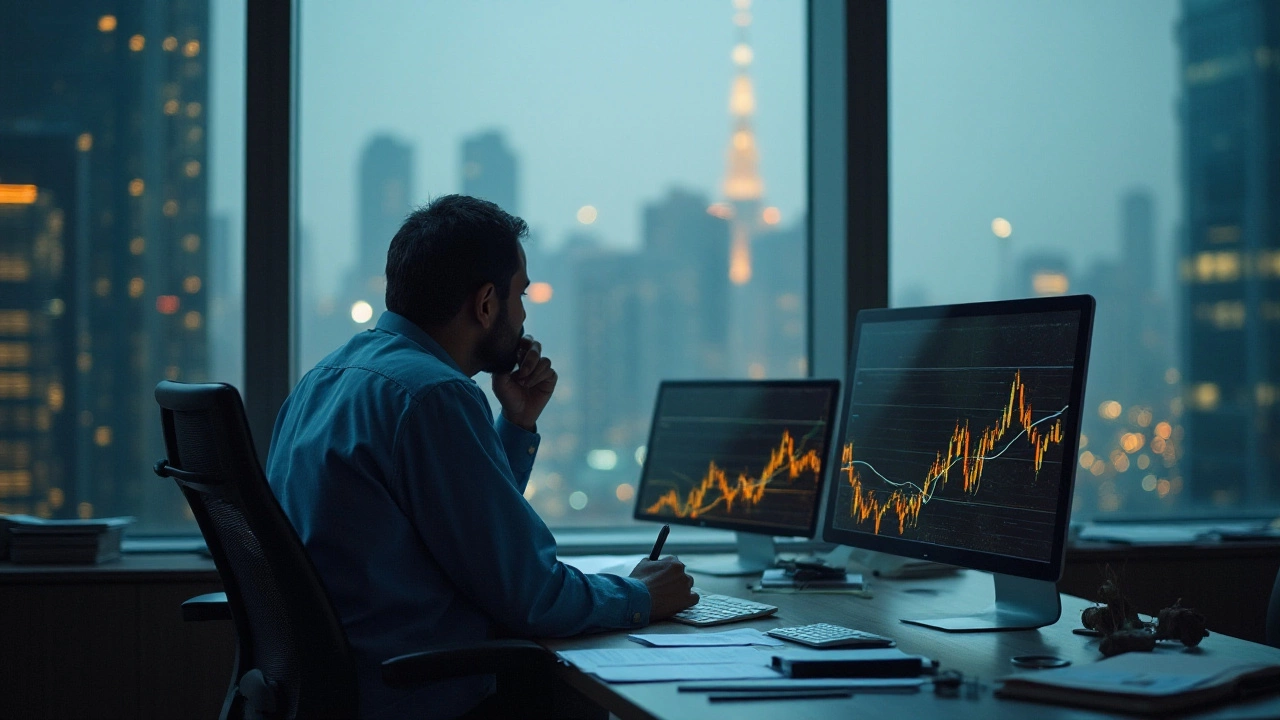
Causes of the Shortages
The chemical shortage that India is experiencing in 2024 is not a phenomenon that sprung from a single issue; rather, it's the culmination of various intertwined factors. First and foremost, disruptions in the global supply chain have played a critical role. With shipping routes still recovering from past global crises and an unexpected surge in demand as industries ramp back up, bottlenecks have become almost inevitable. These logistical challenges aren't just affecting India; they resonate worldwide, reshuffling the playing field for many industries dependent on timely supplies.
Adding to the complexity are geopolitical tensions that have ripples impacting trade agreements and cross-border flows of goods. Trade policies are under constant evolution, influenced by shifting alliances and political strategies, making predictability a luxury in today's market. As supply chain issues remain a significant concern, companies scramble to adapt to these new norms. Additionally, several essential raw materials used in the production of these chemicals are sourced from politically unstable regions, exacerbating the issue. These developments force India to seek alternatives and develop domestic capabilities to mitigate the reliance on these tumultuous external sources.
Moreover, environmental regulations are tightening globally, urging manufacturers to innovate sustainable practices. While this shift is necessary for long-term environmental well-being, it demands significant investments in technology and infrastructure, which smaller companies may struggle to afford. Consequently, the availability and cost of environmentally compliant raw materials have soared, affecting India manufacturers who operate on thinner margins.
Labour shortages in both skilled and unskilled sectors also contribute to this scenario. With increasing urbanization and changing workforce dynamics, it's becoming harder to maintain a steady supply of labor needed for continuous production. Automation offers some solutions, but the transition requires time and substantial capital, which not every firm can afford.
"The challenge of balancing economic growth with sustainable practices is daunting, but necessary," noted a report by the Confederation of Indian Industry.
Lastly, seasonal factors can have unexpected impacts on production flows. Sudden climatic changes or adverse weather conditions can disrupt production cycles, particularly in industries that are heavily reliant on natural extraction processes. Beyond the immediate term, there is an element of unpredictability to the weather that requires industries to build resilience and be prepared for such eventualities. Addressing these issues is critical for sustaining the chemical industry challenges that India is currently facing.
Strategies for Mitigation
The chemical industry in India is grappling with significant shortages, but industry leaders and policymakers aren't just standing by. They've rolled up their sleeves and are working on dynamic strategies to contain and mitigate these challenges. One key approach involves diversifying the supply sources. By not relying on a single supplier or region, companies can buffer themselves against potential disruptions. This is crucial in today's volatile market, where geopolitical tensions can suddenly cut off resources and wreak havoc on production lines.
Another critical strategy is government support. Indian authorities are stepping up to the plate, providing incentives for local production. This not only boosts self-sufficiency but also creates jobs and strengthens the economy. Tax breaks, subsidies, and easing of regulations for new domestic plants are just a few measures being considered to spur growth in the chemical sector.
Technological innovation cannot be overlooked either. Advanced analytics and AI are being employed to optimize supply chain management, predicting shortages before they happen and allowing companies to adjust their strategies in real-time. A report from McKinsey suggests that companies investing in AI-driven supply chain tools see operational cost reductions by up to 15%. This transformation is not a future fantasy but is actively being implemented in India's supply chains to tackle the chemical shortfalls.
"Resilient and agile supply chains are no longer a competitive advantage. They're critical to survival," a report by McKinsey highlights the importance of adaptive methods in today’s global economy.
Chemical shortage India is a pressing concern, but with these combined efforts, companies are not just coping, but setting a new standard for how to manage supply chain challenges. Open dialogue with international partners also plays a pivotal role. Creating partnerships and joint ventures with foreign companies enables technology transfer and mutual benefit, a tactic that the Indian chemical industry is increasingly employing to sustain its competitive edge.
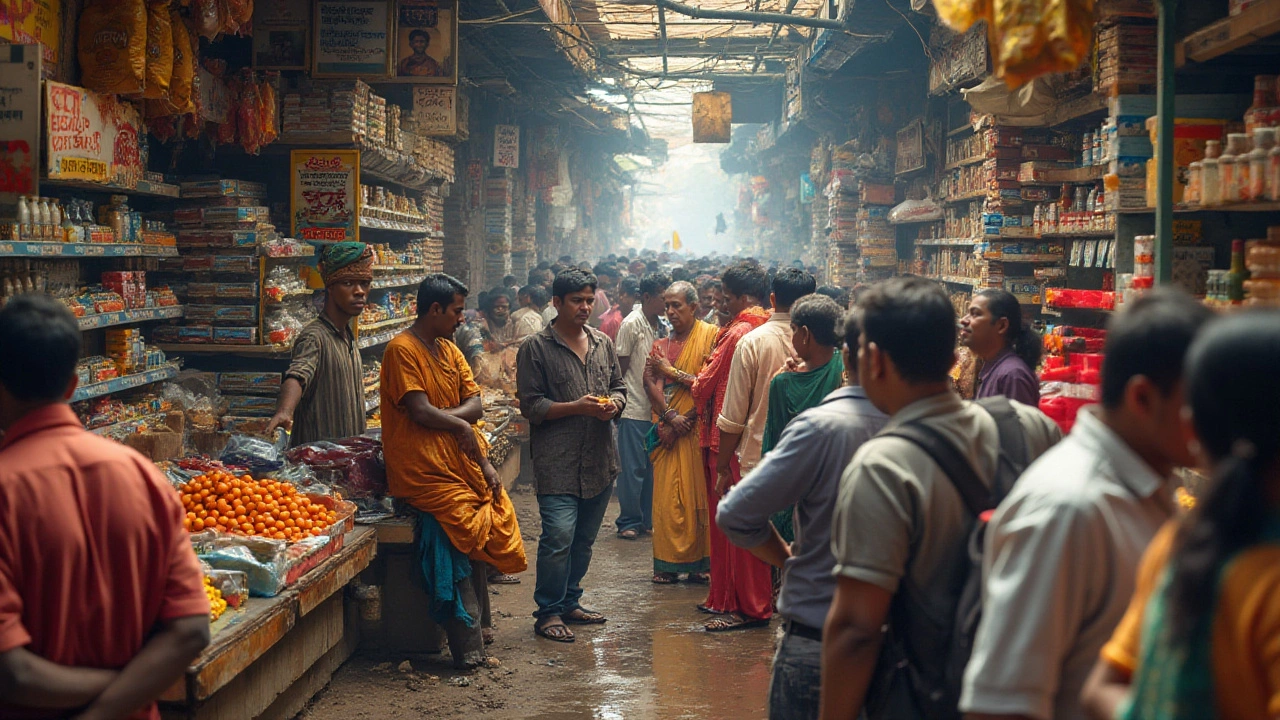
Future Outlook
As we gaze into the horizon of India's chemical industry, there is an equal measure of optimism and caution to be observed. The challenges posed by the current chemical shortage in India are momentous, yet they offer a unique opportunity for innovation and restructuring that could redefine the industry for years to come. Many experts believe that addressing these shortages could spur transformative changes that enhance resilience and sustainability across the board. Given the complexities of current global supply chain dynamics, industry leaders are increasingly looking at technology-driven solutions and localized production models as feasible paths forward.
One potential growth avenue is the investment in digital technologies such as artificial intelligence and blockchain to enhance supply chain transparency and efficiency. According to industry reports, implementing these technologies can reduce lead times and buffer against disruptions like the ones seen during the pandemic. Moreover, the diversification of supply sources by forming strategic alliances with other countries can also help mitigate risks associated with geopolitical tensions. This approach could strengthen the independence and reliability of India's chemical manufacturers, ensuring they remain competitive in the global marketplace.
With sustainability becoming a key driver in many industries, there is also a notable shift towards greener and more sustainable chemical production processes. This shift is not only a response to consumer demand but also a necessity in meeting international environmental standards. "Innovation in green chemistry not only helps protect our planet but could also give India a competitive edge," remarked Dr. Amit Kapoor, a leading chemical industry analyst.
"The transition to sustainable practices within the chemical industry is an arduous journey, but a necessary one if we aim to future-proof our markets and continue growth," he says.
The government of India has rolled out various initiatives, supporting research and development in the chemical sector, indicating a positive future outlook. These measures are designed to stimulate local production, reduce dependency on imports, and promote waste reduction through recycling and efficient by-product management. As these initiatives gain traction, small- to medium-sized enterprises will likely benefit the most, leading to increased employment opportunities and economic growth in the region.
The long-term success of these strategies will hinge on the industry's ability to adapt to rapidly changing market conditions and regulatory landscapes. As India navigates these turbulent waters, the resilience and ingenuity shown by its chemical sector could stand as a testament to the country’s legendary capacity for reinvention and growth. The roadmap ahead involves not just overcoming the present shortages but laying the groundwork for an industry that is robust, adaptable, and sustainable, ensuring India's position as a global leader in chemical production.