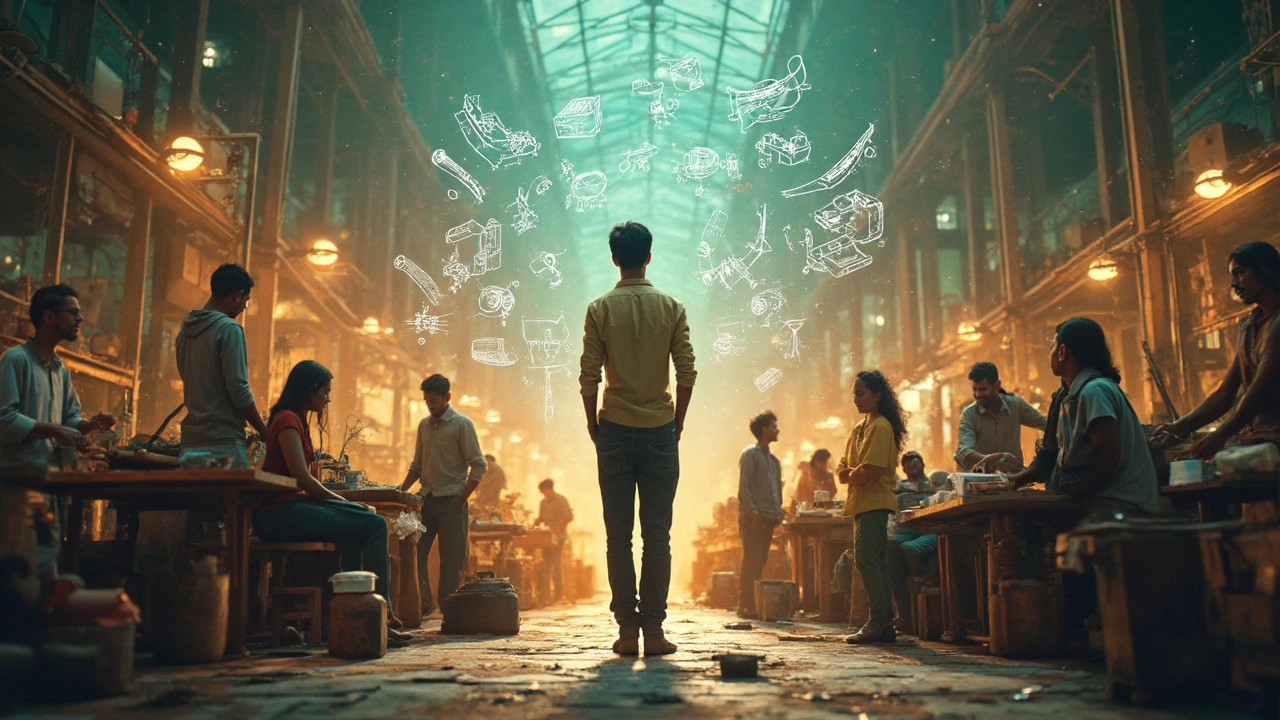
Getting a product from a mere idea to something you can touch and see is no small feat. If you're thinking of jumping into the manufacturing game, understanding the steps is absolutely essential. Just like you wouldn’t build a house without a blueprint, you can’t manufacture a product without a plan. So, let's look at the stages that take a bright idea to the production line.
First off, we start with concept development. This is the phase where your idea is not just a random thought in your head but something you start to give shape to. You’ll want to flesh it out; think about who it’s for, what problem it solves, and why anyone needs it in the first place. Real talk, if you don't have a solid concept, everything else is downhill from there.
- Concept Development
- Design and Prototyping
- Sourcing and Material Acquisition
- Production Planning
- Manufacturing and Assembly
- Quality Control and Testing
- Packaging and Distribution
Concept Development
Concept development is your first big step in the manufacturing process, and it’s all about fleshing out those wild ideas into something real. It's like putting foundation stones down for a house. Fail here, and the whole thing's shaky. But get it right, and you're off to a flying start.
Identify the Problem
The whole point of creating something new is to solve a problem or fill a need. Start by diving into the problem you're trying to address. Ask yourself: What's missing in the current landscape? Who will benefit from your product? Are there similar solutions out there, and how's yours different? Competitive advantage is key.
Research Your Market
You’ve got a problem worth solving, but do people feel the same way? Market research is your friend here. Dig into customer needs, pain points, and existing market solutions. Surveys, focus groups, and even simple internet searches are great ways to gather insights. Plus, understanding your target audience now saves headaches later.
Ideation and Brainstorming
Once you've identified your market, it's time to get creative. Consider different ways to address the problem you've pinpointed. Use brainstorming techniques like mind mapping or free writing. In this stage, every idea is a good one—even if it's crazy! You never know what overlooked nugget might be gold.
Validate Your Idea
A neat trick to avoid going down the wrong path is early validation. Build simple models or simulations and test them with your target audience. This could be as simple as sketching on paper or making a digital mock-up. The goal is to find out whether people are ready to pay for what you're offering.
Remember, the concept development stage is vital. It sets the tone for all the production steps that follow. Nailing this stage means you've got a clear, validated direction before pouring resources into the manufacturing plan.
Design and Prototyping
Once you have a solid concept, it's time to move on to design and prototyping. This is where your idea transforms from dreamy sketches to something you can actually hold. It's a crucial step in the manufacturing process because it's your first chance to catch potential flaws.
Designing is more than just looks. It's about functionality, user experience, and material choices. You need to think about how the product will work, the best materials to use, and even how it's going to be assembled. A well-thought-out design can save tons of money and time down the road. Plus, it ensures your product will delight your future customers, not confuse them.
Steps in Design and Prototyping
- Create Initial Drafts: These can be hand-drawn sketches or done using design software. They should detail different perspectives and parts of the product.
- 3D Modeling: Move those sketches to a digital realm with CAD software to visualize dimensions and functionality.
- Prototype Development: Time to bring CAD designs to life! Use materials like plastic, wood, or metal to develop the initial prototype. 3D printing can be a cost-effective way to test designs quickly.
- Testing and Iteration: Test your prototype to identify any design flaws. Get feedback from potential users and iterate if needed. This is where the rubber meets the road, so be ready to make adjustments.
Did you know that nearly 70% of startups feel the burn of costs due to design changes made too late in the game? Fixing mistakes after production starts is like trying to un-bake a cake—it’s not easy and can get expensive real quick. That’s why this step is not just a box to check off but a deep dive into ensuring your creation doesn’t just look good but works well, too.
Prototyping is all about learning and refining. It's your chance to experiment and dive into nitty-gritty details of production steps without blowing your budget. Take advantage of this phase to validate your idea, because trust me, fixing problems in the early stages will save a whole lot of headaches later on.
Sourcing and Material Acquisition
Diving into the sourcing and material acquisition phase is exciting and a tad nerve-wracking. This is where you get to choose materials that will bring your product to life. It’s like being a chef and picking ingredients for a winning dish—a lot rides on getting this part right.
Understanding Your Needs
Start by pinpointing exactly what materials you need. Are we talking metals, plastics, textiles? Each material comes with its set of suppliers, costs, and requirements. Got a list of must-haves? Great. You'll need that to keep everything in scope.
Finding Reliable Suppliers
Sourcing isn’t just about grabbing materials; it's about finding the right folks who can deliver consistently. Establish relationships with reliable suppliers—these guys are going to be your partners. And hey, don’t shy away from negotiations. Price isn’t everything, but it sure is a lot.
- Research potential suppliers online or at industry trade shows
- Get samples to evaluate quality
- Check references or reviews from other businesses
Evaluating Costs and Logistics
Once you have a few solid options, it’s time to crunch some numbers. Consider costs beyond just price per unit—think shipping, taxes, and potential delays. You’d be surprised how these add up, affecting your overall budget.
Material | Average Cost per Unit | Lead Time |
---|---|---|
Aluminum | $2.50 | 3 weeks |
Plastic | $1.20 | 2 weeks |
Sustainability and Ethics
Today, customers care about where their products come from. Be upfront about sustainability and the ethics of your supply chain. This not only helps the planet but could earn you major brownie points with your buyers.
Sourcing right means you're setting a steady foundation for your entire manufacturing process. Get this right, and you’re one step closer to production success.
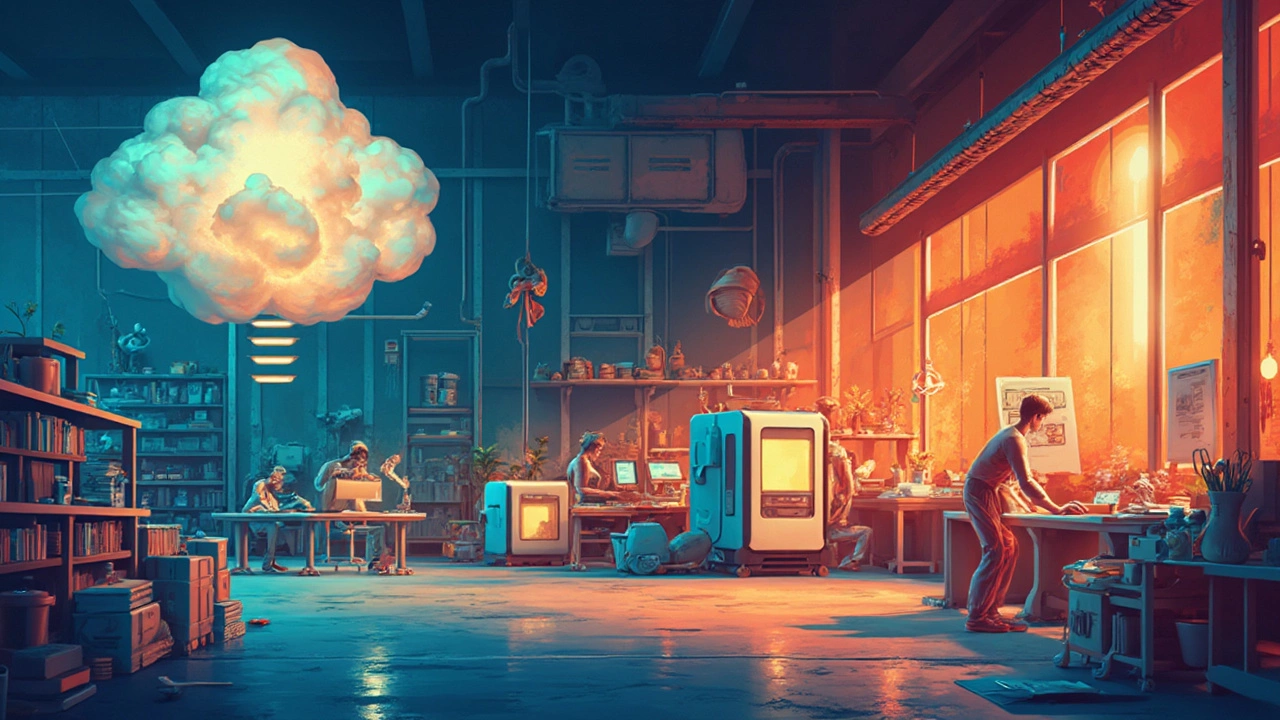
Production Planning
Production planning is where the rubber hits the road in the manufacturing process. You have your concept, design, and source materials, now it’s time to put it all together in one cohesive plan. This stage is all about ensuring that production runs smoothly and efficiently while optimizing resources and minimizing waste.
Define Your Production Goals
Start by setting clear production goals. How many units are you aiming to produce, and by when? Answering these questions will help you design a timeline and allocate the right amount of resources.
Create a Detailed Timeline
A detailed timeline is essential to keep everyone on the same page. It should include start and end dates for each production phase, key milestones, and deadlines. Remember, it’s not just about sticking to dates but keeping quality in check while doing so.
Resource Allocation
Allocate your resources wisely. This means assigning tasks to the right team members, ensuring you have enough workforce, raw materials, and equipment ready to go. It’s also wise to have a backup plan in case any of these resources become unavailable.
Risk Management
Risks in manufacturing can't be ignored. Create a risk management plan to identify possible hiccups and outline strategies to handle them. This could include equipment failure, supply chain disruptions, or human resource issues.
Aspect | Common Risks | Mitigation Strategy |
---|---|---|
Supply Chain | Delays in material supply | Multi-source suppliers |
Workforce | Insufficient workforce | Flexible staffing |
Quality Control | Defective products | Regular quality checks |
Monitor Performance
Once production is underway, you need to monitor performance. Track key performance indicators (KPIs) such as production rate, defect rate, and resource usage. Regular assessment helps in identifying areas for improvement and ensuring the plan stays on course.
By nailing down your production planning, you're laying the foundation for a successful manufacturing line. It might seem like a daunting task, but with careful planning, you’ll avoid many potential pitfalls and keep everything running like a well-oiled machine.
Manufacturing and Assembly
So you've got your designs ready and materials in hand, now it's time for the real action—manufacturing and assembly! This stage is where all the preparation comes together to bring your product to life. It's the heart of the whole production process.
First up is setting up your production line, and this isn’t as intimidating as it sounds. Depending on your product, it might be as simple as organizing your workspace to maximize efficiency or ensuring all your tools and equipment are in top-notch condition. Keep in mind, having a seamless production plan saves you tons of time and headaches down the line.
Start with the Basics
Got the setup? Great, let's talk about the basics of assembly. For smaller runs, you might be doing this yourself or with a small team. Either way, make sure clear instructions are available for every step. Miscommunication can lead to mistakes, and trust me, nobody wants a batch of products with flaws.
Assembly Line Techniques
If you're diving into larger-scale production, consider assembly line methods. Breaking down the assembly into simple, repeatable tasks can hugely boost efficiency. Studies show that even a modestly organized assembly line can increase production by up to 50%. Plus, it reduces the monotony for workers because they master one task at a time.
Here’s a quick snapshot of how a typical assembly process might look:
- Preparation of individual parts or components.
- Initial assembly of components.
- Testing each assembly to ensure it meets set standards.
- Final assembly of the product.
- Quality checks before packaging.
Quality is Key
Now, during this stage, it’s crucial to keep a keen eye on quality. Poorly assembled goods equate to unhappy customers. Regular checks can help catch these issues before they leave the factory floor. Implementing quality control measures doesn't just prevent mistakes—it builds trust with your customers.
Remember, these steps might vary depending on what's being manufactured, but the core idea remains the same—efficient, effective, and quality-focused production. Getting this stage right is the difference between products that fly off the shelves and those that gather dust in a warehouse.
Quality Control and Testing
Quality control and testing are hands-down some of the most critical parts of the manufacturing process. It’s the stage where you make sure your product doesn't just look good, but it performs and lasts as intended. No one wants to spend on a broken gadget or a wobbly piece of furniture, right?
Why Quality Matters
Let's face it, today's customers are picky, and they have every right to be! With options galore in the market, one slip-up could send them straight to your competitor. Reliable quality checks help keep your errors to a minimum and satisfaction levels up. Plus, consistent quality means fewer returns, complaints, and the delightful bonus of positive reviews. Remember, a reliable product is key to keeping your reputation intact.
Testing Phases
Manufacturing's quality control involves several layers of testing. Here's what you usually tackle:
- Initial Checks: This happens at the beginning of production. It’s about making sure raw materials and components meet your standards before they become part of your product. Better safe now than sorry later!
- In-Process Testing: No point waiting until the end. You want to spot and fix issues right as they crop up. This step makes sure that every unit coming off the line is on point.
- Final Inspection: The moment of truth! This is where you check the finished products against that blueprint you’ve been working with since day one. Random sampling can really save the day here.
Tools and Techniques
Tech plays a pretty big role in modern quality control. From simple snap gauges to advanced 3D scanners, various tools help detect flaws, measure dimensions, and test functionality. Also, depending on your industry, there might be specific standards like ISO 9001, which guide the testing processes.
Startup manufacturing processes can often benefit from automating tests to speed things up and reduce human error. Once you're scaling up, even small inefficiencies can hurt your bottom line.
Testing Data
If you’re a numbers person, collecting data is your friend. While it’s hard to generalize due to the variation in industries, reports suggest that up to 80% of defects are found in just 20% of processes. Imagine what eliminating those could do for your efficiency and cost!
Stage | % of Total Defects | Common Causes |
---|---|---|
Initial Checks | 10% | Poor Material Quality |
In-Process Testing | 70% | Machine Errors, Misalignment |
Final Inspection | 20% | Assembly Mistakes |
Ultimately, putting in the effort in the quality control stage can set your manufacturing startup miles apart from the rest. It's about building trust with your customers and ensuring they’re thrilled with what you’re offering. A meticulous approach can save money, stave off customer complaints, and best of all, let you sleep easy knowing every item out the door holds up to your promise.
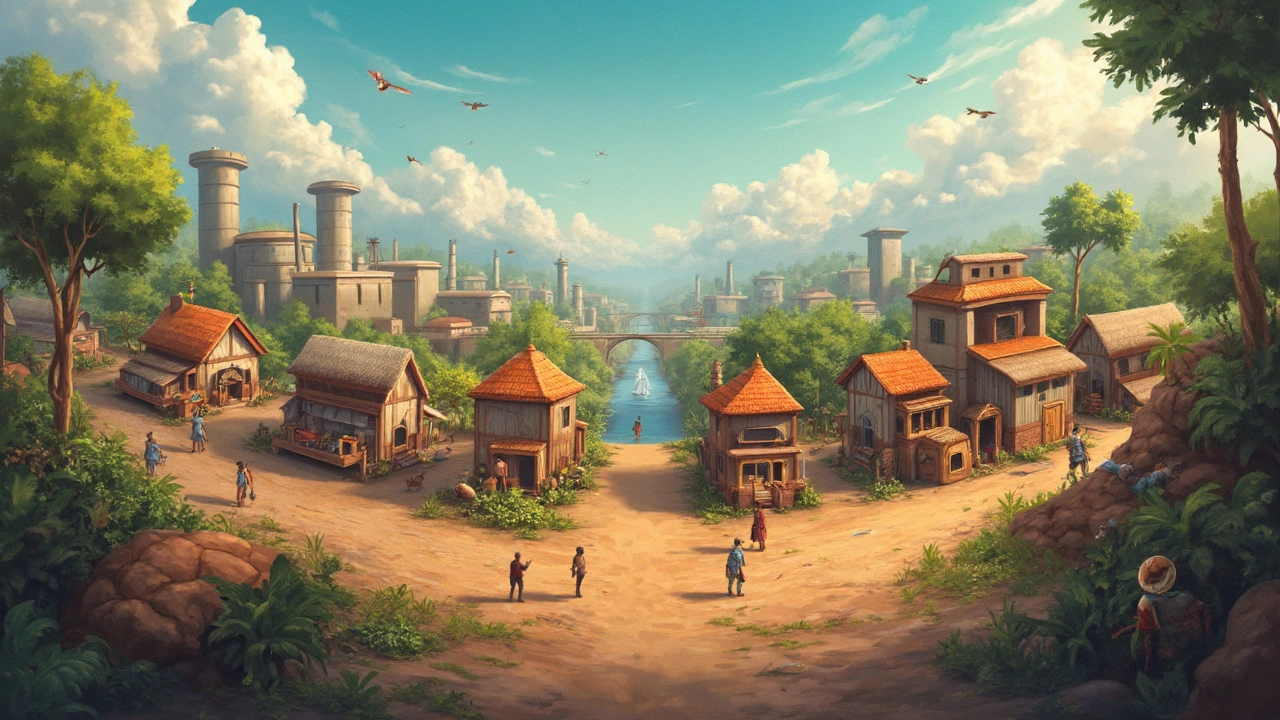
Packaging and Distribution
So, you've got your product all set and ready to roll off the assembly line, but wait—it needs packaging. Packaging isn't just about slapping a label on; it's a crucial part of the manufacturing process. A well-designed package not only protects your product but also communicates your brand, appealing directly to your target market.
Packaging Design
Your package is often the first interaction a customer has with your product. It's worth investing time and resources to get this right. The design should reflect your brand's values and appeal to your audience while also being functional. Ask yourself: Does it protect the product? Is it environmentally friendly? Is it user-friendly? Think of Apple products—clean, simple, and effective packaging that speaks to their product quality.
Choosing the Right Materials
Material choice is just as critical. You’ll have options like cardboard, plastic, glass, and more. Each comes with its own set of pros and cons related to cost, durability, and sustainability. If your audience cares about the environment, opting for eco-friendly materials can set you apart from the competition.
Distribution Strategies
Once your product is all packed up, it needs to get to your customers. Distribution isn't just about shipping; it's about getting the right product to the right place at the right time. Whether you go for direct distribution, retailers, or online platforms, it's key to plan a strategy that aligns with your business goals.
Consider a mix of channels for a broader reach. Online sales are booming, so don’t miss out. However, having a couple of physical locations can boost trust and credibility, especially for a startup manufacturing brand.
Distribution Costs and Logistics
Let’s talk numbers. Distribution costs can add up quickly, including shipping fees, warehousing, and handling. Do your homework. Compare different logistics companies for the best rates but remember, cheaper isn't always better. Reliable service and timely delivery can drastically impact customer satisfaction.
Cost Element | Proportion of Total Cost (%) |
---|---|
Packaging | 15% |
Shipping | 40% |
Warehousing | 30% |
Handling | 15% |
By mastering both packaging and distribution, you’re not just getting your product to market; you're increasing its chance for success. It's about efficiency, reliability, and making that final impression count.